Streamlining Your Stock: Essentials of Reliable Inventory Management Website Design
In the fast-paced world of inventory management, a well-designed website can make all the difference. Streamlining Your Stock is a guide to creating a reliable inventory management website that not only looks good but also enhances functionality. With a focus on user interface design, data integration, SKU management, stock rotation, and technological solutions, this article will provide insights into the essentials of crafting a system that works seamlessly for businesses of all sizes.
Key Takeaways
- A user-friendly interface with a clean dashboard, searchable list views, and efficient form views is essential for inventory management website design.
- Real-time inventory insights, seamless integration with wholesale and e-commerce platforms, and leveraging ERP and WMS systems are key for comprehensive management.
- The use of unique SKUs enhances fulfillment accuracy and simplifies stock tracking, while consistent SKU formats and regular reviews aid in trend analysis.
- Regular stock rotation is critical, especially in the food industry, to minimize waste and maintain product freshness, supported by a well-designed SKU system.
- Choosing the right inventory software, integrating with platforms like Shopify, and implementing automation and regular audits are vital for inventory optimization.
Designing the User Interface
Dashboard Essentials for Quick Overview
A well-designed dashboard is the nerve center of any inventory management website, providing a quick overview of key metrics at a glance. Responsive design is crucial for optimal user experience on all devices, ensuring that the dashboard is accessible and functional, whether on a desktop or a mobile phone. High-quality visuals are not just aesthetic; they play a pivotal role in showcasing your inventory fleet effectively.
User-friendly features such as drag-and-drop editing tools simplify website management, allowing for easy customization and control over the data presented. Here’s a quick list of dashboard essentials:
- Custom Reports: Generate timely, business-specific reports.
- Scheduled Emails: Automate report sending for consistent updates.
- Chart Widgets: Translate complex data into easy-to-understand charts.
With these tools, your dashboard becomes a powerful command center. You’ll identify trends, track performance, and forecast needs with ease.
Remember, the goal is to make inventory management as efficient as possible. Minimizing the number of fields for quick data entry and ensuring clear labeling are just as important as incorporating bold buttons for common actions.
Optimizing List Views with Search and Filters
Effective inventory management websites prioritize speed-optimized performance and a customizable user experience. By integrating advanced search and filter options, users can swiftly navigate through extensive product lists, ensuring a user-friendly interface that enhances customer satisfaction and operational efficiency.
- Advanced Search: Allows users to quickly find specific items using keywords or phrases.
- Dynamic Filters: Enable users to refine product lists based on various criteria such as category, price, or stock levels.
- Sort Functionality: Provides the ability to order products by relevance, popularity, or other predefined metrics.
By streamlining the list view, logistics websites not only improve the user experience but also facilitate better financial tools and decision-making processes for inventory management.
Streamlining Form Views for Efficient Data Entry
Efficient data entry is a cornerstone of effective inventory management. Minimizing the number of fields in form views is essential to speed up the process while maintaining accuracy. By focusing on the most critical information, users can quickly add new inventory items without being bogged down by unnecessary details.
Streamlined forms not only save time but also reduce the likelihood of errors, which can be costly in inventory management.
Consider implementing the following best practices in your form design:
- Use pre-designed forms to guide users through the data entry process.
- Ensure real-time data syncing to keep inventory levels accurate.
- Implement data validation rules to maintain consistency in entries.
- Personalize views based on user roles to enhance the user experience.
By integrating these elements, businesses can create a user interface that supports real-time tracking, multi-channel management, and customized reporting—key features that are crucial for staying competitive and efficient.
Intuitive Layout and Clear Labeling
An intuitive layout paired with clear labeling is the cornerstone of a user-friendly inventory management website. Navigation should be a seamless experience, guiding users through the site with ease and clarity. This approach not only enhances the user experience but also reduces the learning curve for new users.
- Dashboard: Keep it clean and readable, providing an overview of key metrics at a glance.
- List Views: Include search and filter options to review detailed entries efficiently.
- Form Views: Minimize fields for quick entry and ensure that each label is self-explanatory.
The goal is to make inventory management tasks as straightforward as possible, allowing users to focus on their work rather than on how to use the website.
By adhering to best practices in layout and labeling, businesses can streamline their operations and facilitate quick and accurate inventory management. This is not just about aesthetics; it’s about creating a functional space that resonates with the end-user’s needs.
Incorporating Bold Buttons for Common Actions
In the realm of inventory management, efficiency is paramount. Bold buttons serve as visual cues that guide users to perform common actions swiftly. These buttons should be strategically placed and designed to stand out, ensuring that tasks such as updating stock levels, placing orders, or generating reports are completed with minimal effort and time.
- Update Stock: Quickly adjust inventory counts.
- Place Order: Reorder stock before it runs low.
- Generate Report: Access analytics and insights.
By prioritizing the user’s most frequent actions, a website can significantly enhance the productivity of its inventory management system. Bold buttons not only reduce the cognitive load but also streamline the workflow, leading to a more satisfying user experience.
It’s crucial to balance aesthetics with functionality. Buttons should be large enough to be easily clickable, yet not so dominant as to overwhelm the interface. Consistent use of color, shape, and size across buttons will help users form a mental model of the interface, making navigation intuitive and reducing the learning curve.
Integrating Data Sources for Comprehensive Inventory Management
Real-time Inventory Insights for Various Industries
Harnessing real-time inventory insights is pivotal for businesses across various industries to maintain operational efficiency and customer satisfaction. By integrating data from multiple sources, companies can achieve a comprehensive view of their stock levels, enabling agile decision-making and strategic logistics planning.
- Distribution: Precise product tracking and inventory insights in real time
- Manufacturing: Complete overview of the manufacturing process
- Wholesale: Live inventory overview across multiple locations
- Hybrid: Efficient production management with streamlined inventory
Real-time visibility into inventory levels allows businesses to respond quickly to market demands, ensuring that the right products are available at the right time.
B2B inventory management is crucial for operational success, leveraging software development and mobile solutions for real-time data access and strategic advantage in logistics. This approach not only minimizes waste but also ensures that products remain fresh and safe for consumption.
Seamless Wholesale Inventory Management
Wholesale inventory management is a critical component for businesses that need to maintain a live overview of their stock across multiple locations. Real-time inventory insights and precise product tracking are essential for keeping up with the demands of wholesale operations.
- Cloud accounting: Keep inventory and accounting data in sync.
- Warehouse management: Optimize warehouse workflows for peak efficiency.
- E-commerce integration: Seamless connection with platforms like Shopify and WooCommerce.
Now, you have a dynamic inventory system that’s both affordable and efficient, giving you ultimate control over inventory management.
Expert fulfillment services are crucial for e-commerce, integrating ordering systems for efficiency, and ensuring customer service integration. Collaboration and technology are key for logistics success, allowing for a streamlined approach to managing wholesale inventories.
Synchronizing E-commerce Platforms with Inventory Data
In the dynamic world of e-commerce, synchronizing inventory data across platforms is not just a convenience—it’s a necessity for survival. Real-time visibility into stock levels and demand signals is achieved by connecting various systems such as Point of Sale (POS), online order management, and planning engines. This integration allows for agile decision-making and timely insights, ensuring that inventory levels are optimized across all sales channels.
For instance, cloud-based solutions offer seamless integration with e-commerce platforms like Shopify, WooCommerce, and BigCommerce, keeping inventory and accounting data in sync. Warehouse management systems further optimize workflows, contributing to a comprehensive control over stock.
By leveraging tools like Stock Sync, businesses can automate the update of product information and inventory quantities, ensuring accuracy and efficiency. Compatibility with various data formats such as CSV, XML, and API facilitates the import and export process, making inventory management a more streamlined operation.
The synchronization process also involves the standardization of product master data, ensuring that attributes and hierarchies are consistent across all systems. This prevents discrepancies such as inventory records showing availability when physical stocks are depleted. Ultimately, data transparency and governance are crucial for maintaining efficiency and preventing stockouts.
Leveraging ERP and WMS for Business Efficiency
Integrating Enterprise Resource Planning (ERP) and Warehouse Management Systems (WMS) can significantly enhance business efficiency. Utilize WMS for automation, real-time tracking, and order optimization in warehousing. This not only streamlines operations but also ensures that inventory levels are maintained accurately, reducing the risk of stockouts or overstocking.
By optimizing logistics partnerships and integrating technology, businesses can achieve higher service quality and efficiency. Specialized solutions tailored to the unique needs of a company can lead to substantial improvements in supply chain management.
Connecting ERP and WMS systems allows for a seamless flow of information across different business functions. This integration facilitates better decision-making and can lead to cost savings by optimizing inventory holding and reducing manual processes. Here’s how businesses are benefiting from this synergy:
- Real-time visibility into inventory and operations
- Enhanced demand forecasting and procurement planning
- Streamlined order fulfillment and shipping processes
- Improved customer service through timely and accurate deliveries
To fully leverage the potential of ERP and WMS integration, it’s crucial to ensure that the systems are compatible and can communicate effectively. A well-implemented integration can be a game-changer for businesses looking to stay competitive in a fast-paced market.
Inventory Liquidation Strategies and Best Practices
Inventory liquidation is a critical aspect of stock management, particularly when products are overstocked, outdated, or the business is pivoting. Effective liquidation strategies can recover value and free up storage space, ensuring a leaner inventory.
- Identify slow-moving items: Regularly review inventory data to pinpoint items that are not selling as expected.
- Discounting: Implement strategic discounts to encourage sales of overstocked items.
- Bundle products: Create attractive package deals to move multiple items together.
- Online marketplaces: Utilize platforms like eBay or Amazon to reach a wider audience.
- Direct sales: Consider factory outlets or pop-up sales events for direct consumer sales.
By adopting a proactive approach to inventory liquidation, businesses can maximize storage efficiency and maintain a healthier stock level. It’s not just about cutting losses; it’s about smartly reallocating resources to where they can be most effective.
The Power of SKUs in Inventory Management
Enhancing Fulfillment Accuracy with Unique SKUs
The implementation of unique Stock Keeping Units (SKUs) is a critical component in the quest for fulfillment accuracy. By assigning a distinct SKU to each product variant, businesses can drastically reduce picking and packing errors. This precision not only elevates customer satisfaction but also minimizes the need for returns or exchanges due to incorrect orders.
The granularity of SKUs allows for a meticulous approach to inventory management, ensuring that each item, regardless of its variations, is easily identifiable and trackable.
In the context of multi-channel sales, the importance of unique SKUs becomes even more pronounced. They serve as the backbone for a seamless integration across various sales platforms, facilitating a cohesive inventory system. Here’s a quick glance at the benefits:
- Personalized product recommendations based on SKU analysis
- Streamlined returns and exchanges process
- Enhanced insights into sales performance and trends
Ensuring uniqueness across variants is not just a best practice; it’s a necessity for maintaining order within a complex inventory system. A black, size M T-shirt and a red, size M T-shirt, for instance, should have distinctly different SKUs to reflect their color variation, thus avoiding any potential confusion.
Simplifying Stock Tracking for Informed Decisions
Effective inventory tracking is the cornerstone of informed decision-making in any business. Real-time inventory tracking ensures that businesses can respond swiftly to changes in demand and supply, maintaining optimal stock levels at all times. By simplifying the tracking process, companies can reduce the time and effort required to manage their inventory, leading to increased efficiency and reduced costs.
Simplified stock tracking systems empower businesses with the agility to make quick, informed decisions, adapting to market trends and customer demands with ease.
Here’s a basic structure for setting up a simplified tracking system:
- SKU Numbers: Assign unique identifiers to each item.
- Barcodes: Implement scanning systems for quick data updates.
- Inventory Software: Utilize platforms like Appsheet for live inventory data.
By integrating these elements, businesses can streamline their operations, ensuring that they always have the right amount of stock on hand. This not only meets customer needs but also minimizes waste, contributing to a more sustainable business model.
Maintaining Consistency in SKU Formats
Consistency in SKU formats is the backbone of a well-organized inventory system. Decide on a format and stick to it across your entire range to facilitate easier management and tracking. This approach not only simplifies the process for your team but also minimizes errors during stock handling.
Aim for SKU formats that are easy to understand at a glance. For instance, you might start with a brief prefix indicating the product category, followed by digits representing specific attributes like color, size, and an incremental identifier for variations. Here’s a simple breakdown:
- Prefix: Product Category (e.g., ‘TS’ for T-shirts)
- Middle: Attributes (e.g., ‘BLK’ for black, ‘M’ for medium)
- Suffix: Variant Identifier (e.g., ‘001’ for the first variant)
Every product variant should have a distinct SKU to eliminate confusion and ensure individual tracking.
As your business grows, your SKU system should adapt without needing a complete overhaul. Design your SKUs with future expansions in mind, leaving room for additional product lines and attributes. A combination of letters and numbers allows for a higher degree of variation and specificity, which is particularly useful for distinguishing between similar product types or variants.
Regular Inventory Reviews for Trend Analysis
Conducting regular inventory reviews is a critical component of effective stock management. It allows businesses to track performance, anticipate demand, and make informed purchasing decisions. By analyzing patterns in sales and stock levels, companies can adjust their strategies to optimize inventory turnover and reduce excess stock.
Regular inventory reviews enable a proactive approach to managing stock, ensuring that inventory levels are aligned with market trends and consumer behavior.
To illustrate the benefits of trend analysis in inventory management, consider the following table showing a simplified example of inventory review data:
Month | Units Sold | Stock Level | Notes |
---|---|---|---|
Jan | 120 | 150 | – |
Feb | 110 | 140 | Seasonal dip |
Mar | 130 | 160 | – |
Apr | 150 | 170 | Increased marketing |
This table provides a snapshot of how inventory levels and sales can fluctuate over time, highlighting the importance of regular reviews to adapt to these changes. By maintaining a consistent schedule for inventory analysis, businesses can identify trends that may not be immediately apparent, such as seasonal variations or the impact of marketing campaigns.
Implementing Barcode Systems for Automation
Incorporating barcode systems into inventory management is a transformative step towards automation. Barcodes make life easier, enabling quick access to product information with a simple scan. This technology not only speeds up processes like checkout and stocktaking but also significantly reduces the likelihood of errors from manual data entry.
Here are some benefits of leveraging barcode scanning:
- Speed up checkout and stocktaking
- Reduce errors from manual entry
- Track items more accurately
- Ensure consistency and accessibility of data across devices
By syncing data across devices, you eliminate the worry of mismatched stock numbers, providing the same information wherever you are, always at hand, on any device.
Regularly reviewing your inventory is crucial to maintaining an accurate and up-to-date system. Advanced barcode systems can facilitate this by providing real-time tracking and inventory management, which are essential for efficient operations. Moreover, advanced analytics can be integrated to predict and prevent disruptions, ensuring a smooth workflow and reliable data integrity.
Rotating Stock Regularly to Maintain Freshness
Minimizing Waste in the Food Industry
In the food industry, minimizing waste is not only a cost-saving measure but also a step towards environmental stewardship. Effective inventory management is crucial for maintaining a balance between supply and demand, ensuring that food remains fresh and safe for consumption. By implementing just-in-time (JIT) inventory practices, businesses can significantly reduce spoilage and waste, aligning closely with the goals of green inventory management.
Automated inventory management systems are transformative tools in the food industry. They enable precise tracking of stock levels and facilitate the optimization of order sizes, which in turn minimizes waste and maximizes profitability.
Proper storage methods are equally important in preventing food from spoiling prematurely. This not only saves money but also helps in reducing the environmental impact associated with food waste. Regular inventory checks and the use of inventory management software tailored to the food sector can further enhance efficiency and accuracy in stock management.
Best Practices for Stock Rotation
To maintain the highest quality and freshness, especially in the food industry, regular stock rotation is crucial. This involves placing older items at the front and newer stock at the back, ensuring that the oldest stock is used first. This practice not only keeps the inventory fresh but also reduces waste due to spoilage.
Effective stock rotation is not just about maintaining product quality; it’s also about optimizing your inventory levels to meet customer demand without overstocking.
Here are some best practices for stock rotation:
- Always rotate stock based on the ‘First-In, First-Out’ (FIFO) principle.
- Conduct frequent inventory checks to identify and prioritize items that need to be rotated.
- Train staff on the importance of stock rotation and proper handling procedures.
- Utilize inventory management software to track expiration dates and automate rotation reminders.
By implementing these practices, businesses can optimize supply chain processes and create a more efficient inventory system that minimizes waste and maximizes customer satisfaction.
The Importance of Regular Stock Checks
Regular stock checks are a critical component of efficient inventory management. They provide the foundation for accurate records and informed decision-making. By consistently reviewing what’s on hand, businesses can better serve their customers and maintain financial accuracy.
- Accurate records of stock on hand ensure financial and customer service excellence.
- Identifying trends allows for adjustments in ordering and stocking practices.
- Regular reviews of inventory operations can preempt potential issues.
Regular stock checks are not just about counting items; they’re about maintaining the health of your entire supply chain.
Efficient supply chain management websites transform businesses by streamlining operations, optimizing logistics, and strategic planning for cost savings and competitive edge. Regular inventory audits are essential in this process, as they help to spot discrepancies and ensure that the data reflected in the system is up-to-date and reliable.
SKU System Design for Efficient Stock Management
An intelligently designed SKU system is crucial for efficient stock management. By assigning unique SKUs to every product variant, businesses can significantly reduce picking and packing errors, leading to higher customer satisfaction and fewer returns. This precision in tracking inventory levels allows for informed restocking decisions, ensuring that popular items are always available while preventing overstock of slow-moving products.
Creating the perfect SKU system involves a balance of simplicity and intuitiveness. It should be structured to convey meaningful information at a glance, such as product type, size, color, or any other relevant characteristic. Here are some key steps to consider:
- Keep it simple and intuitive: Avoid overly complex codes that could lead to confusion.
- Prioritize scalability: Ensure the system can adapt to future expansions.
- Utilize both letters and numbers: This allows for greater variation and specificity.
- Stay consistent: Use the same format across all product lines to streamline inventory management.
An effective SKU system not only enhances fulfillment accuracy but also optimizes warehouse space and productivity. Strategies like zoned picking and high-density storage, supported by innovations in racking technology, can further enhance supply chain efficiency.
Remember, balancing flexibility and efficiency is key to a successful SKU system that supports your business’s growth and adapts to changing market demands.
Leveraging Technology for Inventory Optimization
Choosing the Right Inventory Software for Your Business
Selecting the ideal inventory software is a pivotal decision for any business aiming to streamline its stock management. The right software should not only align with your current needs but also scale with your business growth. Consider factors such as ease of integration, user-friendliness, and the ability to provide real-time inventory insights.
When evaluating options, prioritize software that offers customization to fit your unique business processes.
Here’s a quick checklist to guide your selection:
- Assess your business size and inventory complexity
- Determine the must-have features for your operations
- Check for compatibility with existing systems
- Look for software with robust reporting and analytics
- Ensure there is reliable customer support and training resources
Remember, the goal is to find a solution that not only manages your inventory effectively but also contributes to overall business efficiency. Take the time to explore and compare different software options to make an informed decision.
Integrating Inventory Management Tools with Shopify
Integrating inventory management tools with Shopify can transform the way you handle stock for your e-commerce business. Shopify’s compatibility with a range of inventory management applications ensures that you can find a solution tailored to your specific needs, from forecasting to fulfillment services.
- Inventory Forecasting
- Order & Customer Management
- Shipping & Fulfillment
- Payments & Financials
These categories encompass a variety of tools that work seamlessly with Shopify, providing an added advantage over other platforms. With features like real-time inventory insights, accurate tracking across sales channels, and synchronization with accounting data, these integrations offer complete inventory control.
By leveraging the right Shopify-compatible inventory management tool, businesses can streamline their operations, reduce manual errors, and maintain a clear overview of stock levels.
Choosing the right tool involves considering your business’s unique requirements. A 14-day trial period is often available, allowing you to test the tool’s effectiveness in tackling the challenges your business faces. Guided onboarding is also provided by many services to ensure a smooth transition.
Automating Inventory Processes with Bsale and Other Solutions
In the realm of inventory management, automation stands as a beacon of efficiency. Cloud-based inventory management systems offer real-time tracking, mobile solutions, and visibility technology to enhance coordination, reduce warehouse costs, and improve profitability through efficient supply chain shifts. Bsale, for instance, provides a robust integration with Shopify, streamlining inventory and document management to ensure accurate operations.
Automation not only saves time but also brings precision to inventory control. By implementing solutions like barcode systems, businesses can maintain an organized and automated inventory.
Selecting the right tools and add-ons is crucial for optimizing inventory processes. Consider the following benefits of inventory automation:
- Inventory Forecasting
- Order & Customer Management
- Shipping & Fulfillment
- Payments & Financials
Evaluating the impact of these automated solutions on your business is the next step. Regular inventory reviews are essential to ensure accuracy and to make necessary adjustments for continued growth and efficiency.
Regular Inventory Audits for Accurate Record-Keeping
Conducting regular inventory audits is a cornerstone of maintaining a healthy stock level and ensuring the accuracy of inventory records. Regular audits allow businesses to detect discrepancies early, preventing stockouts and overstock situations that can lead to financial losses or dissatisfied customers.
By implementing a systematic approach to inventory audits, companies can streamline their operations and maintain a clear picture of their inventory health.
Here are some key benefits of regular inventory audits:
- They provide a clear and accurate record of inventory, crucial for financial reporting and customer service.
- They enable the identification of manufacturing and sales trends, allowing for better forecasting and stock adjustments.
- They facilitate the early detection of potential issues, minimizing the risk of serious problems.
It’s essential to integrate inventory audits into the regular business cycle. This practice not only supports strategic decision-making but also reinforces accountability and control within the inventory management process.
In today’s competitive market, leveraging technology for inventory optimization is crucial for the success of logistics companies. At MasteringAgency.com, we specialize in creating custom logistics solutions that streamline your operations and enhance your digital presence. Our strategic, data-driven approach ensures that your inventory management is efficient and your customer satisfaction is high. Don’t miss out on the opportunity to transform your business. Visit our website and book your free consultation today to start optimizing your inventory with the best in the industry!
Conclusion
In conclusion, designing a reliable inventory management website requires a meticulous approach to user interface design, data integration, and inventory control practices. By focusing on creating a user-friendly experience, integrating real-time data sources, and employing strategies such as regular stock rotation and intelligent SKU systems, businesses can streamline their inventory processes. Consistency, accuracy, and regular reviews are the cornerstones of effective inventory management. Implementing these essentials will not only improve operational efficiency but also enhance customer satisfaction and drive business success. Remember, a well-designed inventory management system is not just about keeping track of stock; it’s about optimizing the entire supply chain for better performance and profitability.
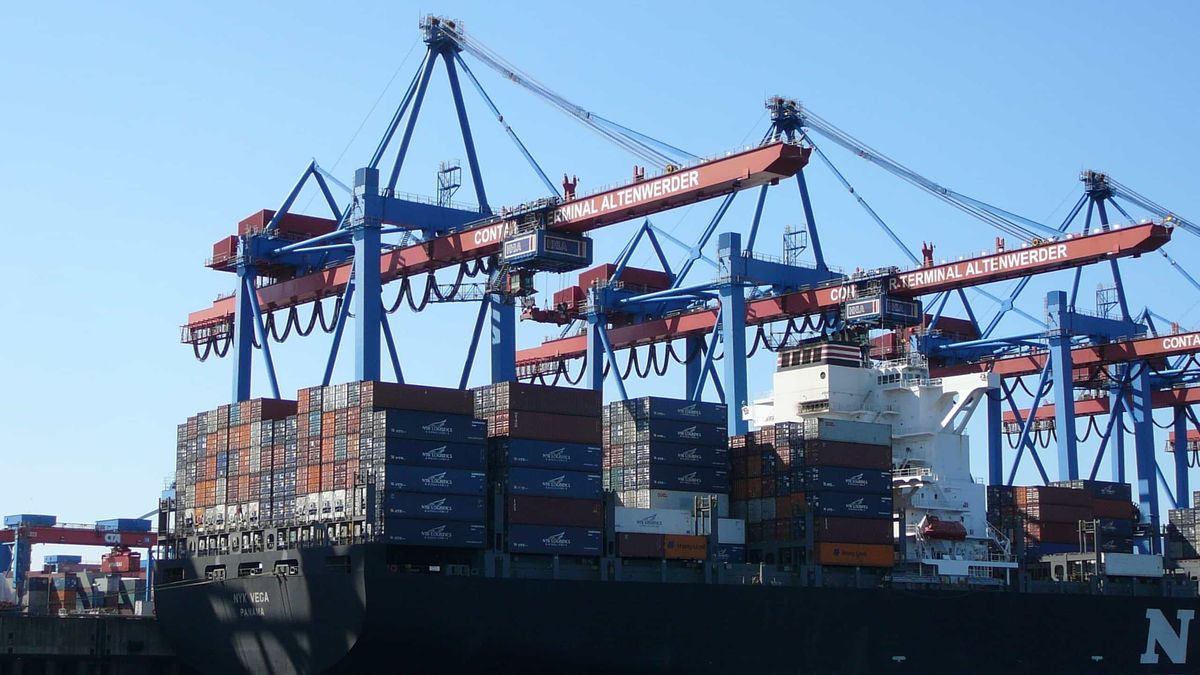